
Most loudspeaker companies tend to take an evolutionary approach to product development; they use the same basic design and refine it over time, a bit like a BMW 3 Series car. This is what B&W has been doing with its 800 series since the Nautilus design came about in 1998. That was the point when the cabinets went from being square to rounded, and the Nautilus ‘head’ was introduced. There have been three iterations of that model, the main change being the gradual introduction of a diamond tweeter across the entire range, starting back in 2005. For the latest D3 800 series models, there has been a ground up revision of pretty much every element of the various models. In fact, the only parts that have carried over from the previous range are the diamond dome itself and the cable terminals, which is good because they were (and are) rather nice.
At a glance, the D3 models look very much like their predecessors, especially the 802, but take a closer look and you’ll see that they are slimmer, deeper, and proportionally different. The ‘head’ is smaller in diameter, but longer and less tapered. Perhaps most significantly, the driver it holds is no longer yellow Kevlar but silver ‘Continuum’, a proprietary material that has been in R&D for several years waiting patiently for the new generation models. The head itself is no longer made of Marlan, but cast in aluminium for greater stiffness where it matters. You wouldn’t think that something as solid as synthetic stone could be vibrated by a relatively small drive unit, but it turns out that Marlan is not very stiff at 2kHz, which is bang in the midrange so crucial to this application. This, like most of the changes made for D3, is a means of reducing cabinet vibration and results in a ‘quieter’ loudspeaker that adds less of its own character to the music.
The cabinets are still made of curved plywood but, and this is strangely not obvious, the curve has been reversed. The bass drivers have to be mounted on aluminium rings to make this work and the open ‘end’ of the U-section woodwork is now covered with a full height aluminium heatsink that holds the crossovers and terminals. Internally the matrix structure that gives the cabinet rigidity has fewer parts but is made from plywood that’s much beefier than the MDF it replaces, they also feature metal parts to provide maximum rigidity at the point where the drivers are fixed. In the past, Bowers & Wilkins has used computer modelling to design its drive units; for D3 this technology has been used on the cabinet as well and this is why the designs have changed so much. The new ‘Turbine’ head is smaller and wider at the back for stiffness; it’s made from a single aluminium casting and has internal bracing in the form of radial fins. To stop it ringing, the whole thing is damped with TPE (thermoplastic polymers), as used in modern Kango breakers.
The change of colour and name of the midrange driver is fairly significant as well; apparently they have been working on Continuum since 2007, but couldn’t get consistent enough results for the 2010 800 series revision. The company now has a patent pending on it. It’s a woven material like Kevlar, but is damped on the back; apparently this makes the midrange faster, has lower noise, and better self-damping. More critical is that Kevlar is anisotropic; its performance depends on the direction of weave. I recall Bowers & Wilkins mentioning that driver orientation is critical and this must be why.
The bass drivers are no longer Rohacell, but consist of carbon fibre skins over a sintactic foam core that the company is calling ‘Aerofoil’. Unlike pretty well any other driver these cones are thicker in the middle than at the in- and outside. This stiffens the cone while keeping weight down and helps to push the first break-up mode to between 400 and 550Hz. The tweeter is still a diamond dome, but it has a new motor assembly, and it sits in a milled aluminium pod that’s shorter than it used to be. It now has a permanent grille to protect the very fragile diamond dome and avoid the thousand pound cost of having it replaced. Apparently, R&D spent many hours sweating over the precise nature of the grille frets or holes, in order to find a design that did not compromise the sound.
I mentioned at the beginning that appearances haven’t changed that much at first glance, but in the case of the 803, that isn’t true. The last example of this model did not have a separate ‘head’, but had the midrange in the same enclosure as three rather than two bass drivers, with only the tweeter pod outside the box. For the new range Bowers & Wilkins have seen fit to make the 803 more like an 802; in fact, it is essentially a compact version of that model with a smaller Turbine head containing a 130mm Continuum mid above two 180mm bass drivers. The 802 on the other hand has a 152mm mid and 203mm bass drivers. The odd thing is that the old 802 Diamond weighed only 10 kilos more than the new 803 D3; the price was very similar, too. The company even claims that the new 803 sounds better than the previous 802, and as I used three generations of that model over many years I can confirm that they aren’t wrong; this thing is a proper ‘OMG’ loudspeaker.
Set up is facilitated by built in rollers that help move the 65 kilo weight of each speaker into place. A set of burly spikes lurk under the plinth and can be screwed down once you have found the optimal position: alternatively leave the spikes locked away and put the speakers on isolation bases for better results.
I’m told that the 803 D3s sound best when bi-wired, but as I have just the one set of Townshend Isolda DCT speaker cable, the supplied bridging cables were connected to get signal to both halves of the crossover; at least they’re not bars or plates. From there on in, these speakers were a revelation: all that R&D work has resulted in a supremely articulate and transparent loudspeaker that exposed unexpected details on virtually everything I played. Steve Pearce from Bowers & Wilkins’ R&D team, who brought the 803s over, likes to play loud – rather louder than me – but it was thrilling to hear such a visceral and at the same time clean sound. The low end coming off of an NAP 250 DR was almost physical. I discovered later that more could be achieved with more power, but the result with only 80 Watts was still an experience. Several albums demanded to be played, including one from Sonny Boy Williamson whose voice, blues harp, and finger clicks were delivered with a realism that belied the age of the recording. It has to be said that this speaker delivers on a visceral level with uncanny calm; that is, they produce a very strong, wide bandwidth sound but stop and start as effortlessly as a compact monitor. Very few speakers can reproduce the power of the double bass on Patricia Barber’s ‘Company’ [Modern Cool, Premonition]without blurring the finger work. You need a grippy amplifier to achieve this but I have one of those in the ATC P1.
I didn’t mention it before but this is a ported speaker; the port points down at the base so you don’t see it and it’s so well tuned that you don’t hear it either. As a long time transmission line user, I have grown sensitized to port character, but couldn’t detect any extra bloom to the bass with the 803 D3. What was easy to hear is supremely articulate, precise, and yet musically fluent sound quality with a range of sources and amplifiers, but this level of transparency means that the less able partnering equipment is very easy to identify. It made abundantly clear that networked digital sources are more musically engaging than USB connected ones for instance, the Primare PRE60 reviewed last month proving its worth with ease in this respect. Herbie Hancock’s version of ‘Ain’t Necessarily So’ [Gershwin’s World, Verve] sounded fabulously open, the sound totally escapes the cabinets and oozes tonal depth across the board while remaining taut and coherent. It’s rare to find a speaker that does bass extension, tonal richness and finesse alongside great timing but the 803 is such a speaker. This comes down to an uncanny degree of low level resolution, a result of all the work that was done to stop the cabinet and drive units from vibrating and masking the signal.
Music reproduction is a forgiving science, even a crude loudspeaker will sound tolerable with most material at average listening levels because the distortions are usually harmonious, meaning they blend in with the signal. But, at the same time very few loudspeakers fool you into thinking that you are hearing the real thing; by reducing the sort of colorations that the majority of loudspeakers add to the sound Bowers & Wilkins has succeeded in making a speaker that gets very close. You need a great recording and replay chain for this to work of course, one that eschews character for neutrality, and does equally as much to keep noise to a minimum, but these exist and this speaker will tell you which ones are doing it the best. I have banged on about the Townshend Allegri passive controller before because I can’t find a better preamplifier and this was proved by comparing it with alternatives through this speaker and confirmed when I discovered that they use the same thing at Bowers & Wilkins R&D dept.
What makes the 803 D3 particularly appealing is the substance that it finds in every recording. If there is the hint of three-dimensionality to be found, you will know all about it. The shape and scale of imaging is precisely rendered, but without any hint of grain or brightness: it’s definition without tears, or the potential for long term listening fatigue. It also picks apart recordings in such a way that you better understand the way they have been made and the ideas behind the music. On Laura Marling’s ‘Friends’ [Once I Was An Eagle, Virgin]the voice is spectacularly real and the multiple layers of guitar opened up and laid bare to reveal the distinct influence of Jimmy Page in his Led Zeppelin III period. You can play such music quietly or at medium levels, but there is a strong urge to wind up the wick. This is largely because there is so little distortion and thus barely any discomfort involved in playing louder. I guess this is the reason why there are bigger models in the range; larger drivers usually equate to higher potential sound pressure and if you have a big room or a big appetite for volume that would be a tempting proposition.
The 803 D3 is a spectacularly good loudspeaker; play anything you know and it will deliver more of the low level detail, more of the physical scale, and more of the heart that the musician(s) who created it put in. You need a reasonable amount of good quality power to induce the speaker to do this and the best source and control equipment that you can find, but so long as the hardware can communicate the important things this B&W will deliver the goods. I’ve said it before but it warrants repeating: if this speaker had a boutique brand on it you’d have to pay two or three times the price to get this degree of transparency, control, vanishing coloration, and outright musical thrill power. But there are no boutique brands with Bowers & Wilkins’ research facilities, so the chances are you will only find serious competition from a few of the larger loudspeaker companies. Even then you will have a long, hard search to find anything that comes close at the price.
TECHNICAL SPECIFICATIONS
- Type: three-way, four-driver, floorstanding speaker with reflex loaded enclosure
- Driver complement: One 25mm diamond dome tweeter; one 130mm Continuum cone FST midrange driver; two 180mm Aerofoil cone bass drivers
- Crossover frequencies: not specified.
- Frequency response: 19Hz – 28kHz
- Impedance: 8 Ohms nominal/3 Ohms minimum
- Sensitivity: 90dB/W/m
- Dimensions (HxWxD): 1160 × 334 × 498mm
- Weight: 65.5kg/each
- Finishes: Piano gloss black, satin white, Rosenut
- Price: £12,495/pair
Manufacturer: Bowers & Wilkins
Tel (UK only): 0800 232 1513
Tags: FEATURED
By Jason Kennedy
More articles from this authorRead Next From Review
See all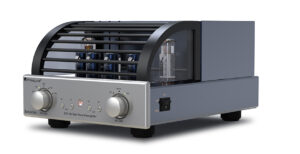
PrimaLuna EVO 100 phono preamplifier
- Apr 22, 2024
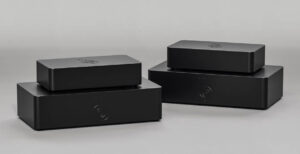
Reiki Audio SuperSwitch Master Pro + Servant Pro
- Mar 27, 2024
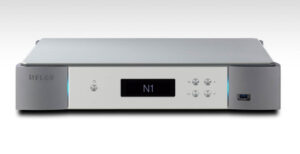
Melco Audio N1-S38 music server
- Mar 27, 2024