
It’s questionable whether this product needs a review in the conventional sense. Just 50 pairs of Magico’s M-Project speakers were made, all of which were sold long before the first model rolled out of the factory. By the time we got to hear them in Lisbon last weekend, the whole story was done and dusted, and even if it were to become a product line, the cost of the speaker is intense enough to make it a tough call to discuss. That said, paying $129,000 for a pair of loudspeakers is, by super-high-end audio standards ‘intense’, but not ‘extreme’.
Of course, in some respects, it’s best discussing this with the engineer, not the oily rag. So, before hearing the M-Pro at its European launch, I spoke with Magico CEO Alon Wolf on the subject:
AS: What was the motivation for the M-Project?
AW: The way this concept started was that we wanted to build a new thing. We’d been working on this tweeter for a couple of years, and this tweeter was the hardest thing we’d ever worked on. We also had new cone material. We also had started working with carbon fibre. But we were not sure where it was going to fit. Is it a Q? Is it an S? Is it something new? So, it was our tenth year anniversary, and we thought ‘Let’s just do a special project, and see where it takes us.’
It’s almost like when you do a concept car: you gather together your current and future technologies, and you show people what you can do, what you should be doing. So we decided to do just that, a kind of a special project, just 50 pairs, and that’s how this thing started.
What technologies separate the M-Pro from existing Magico loudspeakers?
The M-Project has our core technology. It’s mainly an aluminium loudspeaker, but with carbon-fibre sides, which allow you to create the curvature in an easier way than if we made it from aluminium. The carbon-fibre also adds a good amount of damping: it’s basically a carbon wing, so it has a core of foam, which acts as a good damping material to the aluminium enclosure.
We also use the latest and greatest Mundorf capacitors. In fact, we used all of them: we took the entire first and second production of the film that they made for these capacitors. I don’t need to go into the technical detail of what’s better about these capacitors, but they are better, and a great deal more expensive than the already expensive capacitors; but they also add to the mix of the M-Pro.
The most profound difference in the M-Pro, however, is the tweeter. It’s unique in many ways: it’s the first beryllium tweeter to be coated with a five-micron thick layer of diamond. It’s a new dome that took us a long time to achieve because we not only increased the size (it’s a 28mm, in place of a 26mm), it also increased the radius of the dome.
That tweeter was very difficult to develop; I think we broke 10 tools trying to design it, because it’s a very stiff material. Trying to push this material and keep the structure intact was very challenging! But this resulted in a tweeter with a resonant frequency that is pushed up thanks to the diamond without adding any significant weight (because we’ve basically added five microns of carbon), and better power handling (both because it is bigger, and because it has a larger magnet system with more ways to dissipate heat).
The rest of the drivers are unique to the M-Project, although the motor systems are similar to what we have been doing in other models. What’s new on the driver section is the cone. This is our seventh-generation actually; it’s a sandwich cone as we used to make before, but instead of using carbon nano-tubes to enhance the stiffness of the cone, we are using graphene. What that does is reduce the weight of the cone by 30% and yet stiffen it by 300%! We would have never dreamed this would be possible.
That must mean Magico is the first audio brand to use graphene
Not just in audio – I think Magico is the first company in the world to use graphene commercially. The company that supplies graphene to us (we source it from Japan) tell me they are not aware of any product already in the market actually using this. In fact, it wasn’t to be part of the project, but it came available literally while we were closing things up, so we had to reopen the project, which was why there was a delay of almost three months to get the M-Project to market, because I just had to use it once we had the chance to do that.
Using graphene is very expensive, but so is using nano-tubes. The graphene is imbedded in the carbon of the driver itself, which is how we save the weight, because there is a lot of resin involved when using nano-tubes. So, it’s quite an extraordinary thing. And it does improve the sound tremendously. It’s not as revelatory as the tweeter, because the tweeter – at least to my ears – is a new thing. The mid and bass units are just doing what they know how to do, but better… it’s not like the tweeter.
Why do you think the new tweeter is so important?
When you design something like this, you look at the specs and you know it’s going to be better, but you never know what it’s going to mean until you actually hear it. I was expecting the usual thing when you hear a better tweeter: more of this, more of that! But when I first pushed the ‘play’ button and sat down in front of the prototype M-Pro for the first time, I was quite shocked. It had none of what I expected… in fact, I was not hearing the tweeter at all. Everything was there, but there were no ‘highs’. It really threw me. But all the information, the extension was there, and there to the point where you start hearing things you never heard before, especially in terms of tonal colour and harmonic structure of instruments.
It is not like the tweeters we are used to. The violin is more of a violin now, the flute is more of a flute, and doesn’t sound like its trying to be reproduced through the elaborate apparatus of a loudspeaker. We managed to remove a lot of the artefacts that create these ‘highs’ we are all used to from tweeters, and in the process it allows us to get a lot closer to the real experience: if you go to a concert hall, you don’t say ‘oh, listen to the highs!’, you just listen to the music.
This was quite a profound experience to me. I think this is… I don’t want to say a breakthrough – I don’t want to be too dramatic – but it’s a new musical experience, and when you start listening… it’s intoxicating. It’s something we are not used to hearing in audio and only now can I go back and listen to even our own tweeters (which I think are spectacular in their own right) and can hear that they are working very hard to do what they are doing.
Removing that is a new thing!
Back to the enclosure, can you envisage using carbon-fibre in more Magico speakers?
I don’t know yet. It’s a rather costly and complicated process to include. It’s definitely something we’d like to include, but there are other considerations aside from wishes!
You designed the M-Project as a strictly limited-run design. Was that wise?
We built 50 pairs and they were all sold in the first month: sight unseen and unheard. I thought we’d sell maybe 25 pairs and the rest would sell after that, when they were auditioned, but it was all gone in one month. There are some distributors that bought quite a few M-Project, and they might have stocks left, but from our perspective, they’ve all gone. On the one hand, that’s a reassuring feeling, because it means the market has trust in us, but it put a lot of pressure for us to ‘come up with the goods’. Fortunately, I think it all worked out well!
As the M-Project has been so well received, have you considered making a second run?
No. I’m very protective of the M-Pro. This is my gift back to the people who gave us the trust, and paid a lot of money up front for something that really at the time did not exist. It was just a concept coming together.
Will the design of the M-Project influence future Magico loudspeakers?
Of course! In fact, it already has: the Q7 Mk II happened as a direct result of the M-Pro. Magico wasn’t going to do a second version of the Q7 until I heard the top end of the M-Pro. And then I realised we had to. So, that’s the reason we did the Mk II; the tweeter, and the graphene midrange.
We also offer a complete upgrade for Q7 owners, and it’s the same amount of money that adds up to the price of the second one, so we made it fair. It’s still a lot of money, but it’s a big upgrade: you have to send the speaker back and we have to change the faceplate because the tweeter is bigger, it’s a new crossover, and so on… it’s a big job!
And now, it’s my turn to talk!
In fairness, Alon Wolf is one of the easiest people to interview: he speaks in publishable sentences, and if you say “Tell me a bit about your loudspeakers?” he can talk for hours without a break and with a fairly high degree of passion. When it comes to interviewing him, it’s more about getting a word in, and trying to stop him talking before your recorder’s batteries run down or your SD card fills up. But, eventually it was my turn to listen to the loudspeakers.
Faced with the M-Pro as a product in its own right, you get to understand why Alon Wolf is so passionate about that tweeter. A select group of Magico owners and reviewers gathered in Lisbon to listen to the M-Project as it should be heard. OK, so ‘as it should be heard’ meant an absolutely top-notch system comprising Metronome’s top four-box CD player, Constellation Audio’s Reference Class electronics (including the European first listen to the mighty Hercules II stereo power amplifier), and Transparent Audio’s Magnum Opus cables. In other words, audio’s Formula One! The M-Project demands such uncompromising products in partnership, but this is also self-selecting: a $130,000 loudspeaker is unlikely to wind up being driven by a $399 receiver found on eBay.
That tweeter absolutely didn’t sound like a tweeter, because the loudspeaker didn’t sound like audio. It sounded more like the real thing. Yes, we inch closer to this goal with every generation, and yes, audio reviewers tend to hype these incremental steps up, but this one is different; it draws practically no attention to itself. In a way, the performance is that of well-engineered designs (such as the classic BBC loudspeakers, or the likes of those coming from PSB), but with even less coloration and attention drawn to the influence of the loudspeaker.
The resolution on offer here was so significant; it almost made a mockery of what we hear from other systems. One live Mozart recording, you could not only hear two people coughing in the audience, you could not only identify where they were in the physical space, but you could tell one of them was considerably more bronchial than the other. One was polite coughing, the other was ‘have you taken your medication’ coughing. On other systems, you barely hear there is an audience.
So the magic of the Magico is there is no magic – it is all science; just science sufficiently advanced to make it seem like magic to most listeners. The loudspeaker was resolving of system enough to easily hear the difference between digital filters, or switching between triode and solid-state output in the Metronome and throwing a soundstage sufficiently large enough to impose imaging limits at the side-wall diffraction panels, and the sealed-box precision and speed to the bass made it one of the most agile large loudspeakers I’ve heard.
In short, this was one of the most – if not the most – significant audio encounters I’ve had in my career, and those 50 owners are some of the luckiest audio enthusiasts out there.
More importantly though, what’s the point? What is the point of a loudspeaker of this magnitude, if no one else learns from it? This is the reason for this feature; not just to discuss the best loudspeaker you, me, and seven billion other people will never own. Not simply to point out that the audio world ended up being the first place an atom-thick form of carbon called graphene went commercial.
No, the point is, we should all be learning from projects like this one. OK, so graphene and diamond-coated-beryllium are not the stuff of drive units in $400 loudspeakers, but this raises the bar for audio, and everyone should be both pleased at that, and desperately trying to leverage parts of that technology to better their own designs.
In other words, the M-Project is more than a top loudspeaker that falls into the hands of a lucky few dozen well-heeled audiophiles; it’s a $130,000 gauntlet thrown down to the audio world. Are you up for the challenge?
Tags: FEATURED
By Alan Sircom
More articles from this authorRead Next From Blog
See all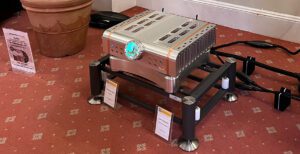
Audio Show Deluxe 2024: A photo show report
- Mar 28, 2024
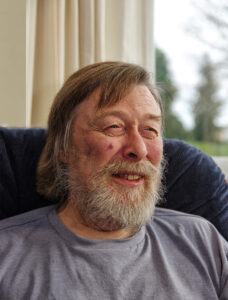
Paul Messenger 1949-2024: A personal tribute
- Mar 26, 2024
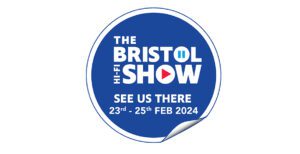
Bristol Hi-Fi Show 2024: See You There!
- Feb 21, 2024
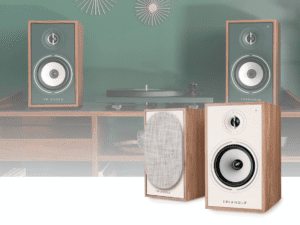
Triangle Borea Connect
- Feb 19, 2024